Why Skipping Routine Fleet Services Can Lead to Expensive Repairs
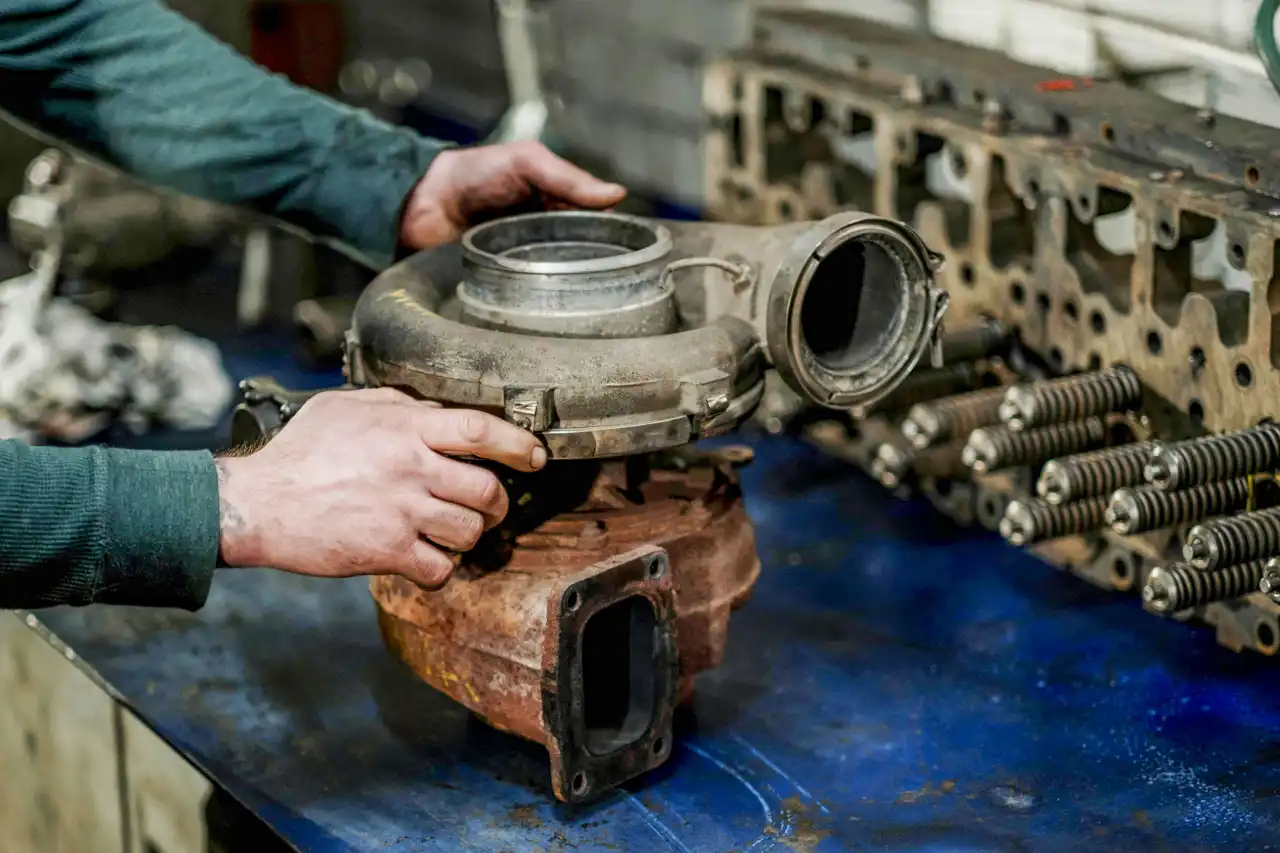
If you’re running a fleet in Chicago’s tough traffic and weather conditions, skipping routine maintenance might seem like a harmless way to save time and money. But here’s the kicker—it’s actually a surefire way to fast-track expensive repairs and unexpected downtime. Let’s break down exactly how neglecting routine fleet services can cripple your operations and cost you more in the long haul.
The Snowball Effect of Skipped Maintenance
A skipped oil change today could mean a seized engine tomorrow.
Seriously, when routine services are overlooked, small issues compound into major breakdowns. For example, old engine oil loses viscosity and its ability to lubricate critical components. Without proper lubrication, metal parts grind against each other, generating heat and wear that leads to catastrophic engine failure.
And that’s just one fluid. Missed coolant flushes can lead to overheating, which warps cylinder heads and destroys gaskets.
Forget to top up transmission fluid? Now you're dealing with gear slippage, hard shifting, or even complete transmission failure—each costing thousands to repair.
Real-World Fleet Failures: A Chicago Perspective
Let’s talk about what happens on the ground. In places like Chicago, where road salt, potholes, and freezing temperatures challenge vehicles daily, routine maintenance isn’t optional—it’s essential.
Without regular air brake inspections, moisture can build up in air tanks and lines, especially if the air dryer fails. That moisture can freeze, causing brake failure. A truck with compromised braking power on icy roads is not just hazardous; it's a lawsuit waiting to happen.
Or consider wheel bearing neglect. Bearing grease deteriorates over time. Once bearings overheat, they can seize up, potentially causing a wheel-off incident, and that is the fastest way to a DOT violation.
Hidden Systems That Need Love Too
Your after-treatment system—EGR, DPF, and SCR—components work quietly to keep your emissions compliant. But when these systems are ignored, carbon builds up in the DPF, sensors fail, and forced regen becomes inevitable. Left untreated, you could be looking at engine derate mode, putting your rig out of commission until it’s fixed, and facing hefty EPA fines for breaching emissions regulations.
Or look at your suspension system. Leaf springs and shocks support your load and control your ride. If a shock absorber fails, it can’t contain rebound, which ruins tire tread and compromises handling. You’ll not only pay for shocks, but you’ll be replacing tires prematurely, too.
The Domino Effect on Downtime and Revenue
Here’s where things really sting: downtime. Every hour a rig sits in the shop instead of hauling freight is lost revenue. Missed deadlines can cost contracts, erode client trust, and force dispatchers to reroute, which throws off the entire logistics chain.
A simple PM service might cost you just $300 and take a few hours. Let that slip and you could be looking at a $12,000 engine rebuild, plus three days of lost income.
Downtime doesn’t just affect the bottom line; it burns morale, frustrates drivers, causes potentially irreversible damage to your reputation, and throws operations into chaos.
Safety, Liability, and Compliance Risks
Skipping fleet services doesn’t just hurt your equipment—it puts lives at risk. Malfunctioning brakes, steering systems, or lighting components increase accident potential. And if an investigation reveals neglect? You could be staring down fines, lawsuits, or even FMCSA penalties.
DOT inspections also become a nightmare. Faulty systems often trigger out-of-service orders on the spot, grounding vehicles until they're repaired. That’s more unplanned downtime, and more cash down the drain.
The Role of Preventive Maintenance Schedules
Routine maintenance isn’t just about fluid top-ups—it’s a comprehensive process that includes inspections, diagnostics, lubrication, cleaning, and replacements. Your preventive maintenance schedule should cover:
- Oil & filter changes
- Brake inspections & adjustments
- Coolant system flushes
- Transmission service
- Suspension & alignment checks
- Air system testing
- Electrical diagnostics
Sticking to these schedules allows your team to catch issues early, plan repairs on your terms, and extend the service life of every truck in your fleet.
Invest in Uptime, Not Damage Control
Here’s the bottom line: it costs far less to maintain a healthy truck than it does to resuscitate a broken one. Routine fleet service is an investment—one that saves you from breakdowns, lost loads, missed deadlines, and busted budgets.
So, don’t treat maintenance like a chore. Treat it like your fleet’s insurance policy—because when one truck breaks down, it’s not just that one truck that’s affected. It’s the whole operation.
Conclusion
In the fast-paced world of logistics, downtime is your worst enemy. Skipping routine fleet maintenance may save you a little time and money upfront, but it opens the floodgates to massive repairs, safety risks, and operational disruptions. Staying ahead with preventive care keeps your trucks rolling, your drivers safe, and your business profitable.
Don’t wait until something breaks—stay on schedule, stay on the road.
Similar posts
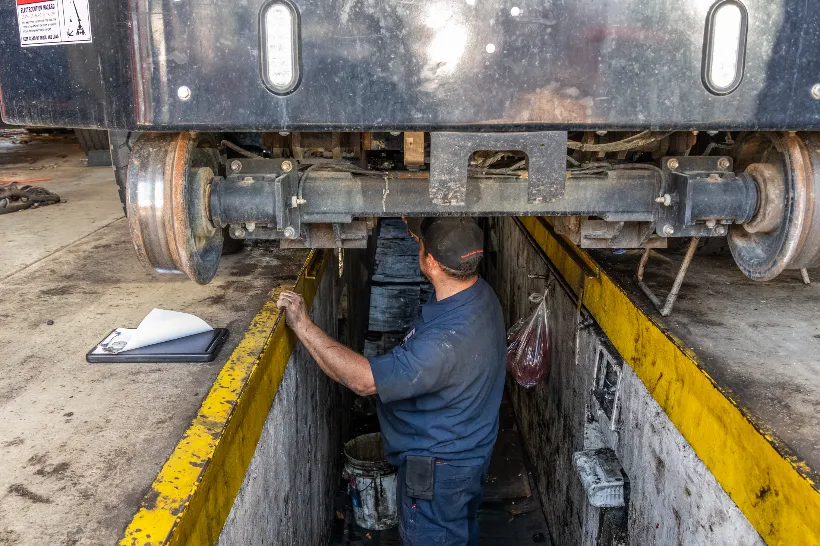
5 Fleet Maintenance Mistakes That Are Draining Your Budget—and How to Fix Them
Fleet maintenance mistakes cost more than downtime—they bleed your budget. From skipped inspections to poor recordkeeping, tire mismanagement, and cheap fixes, here are five costly errors and how to avoid them. Protect your trucks and your bottom line.
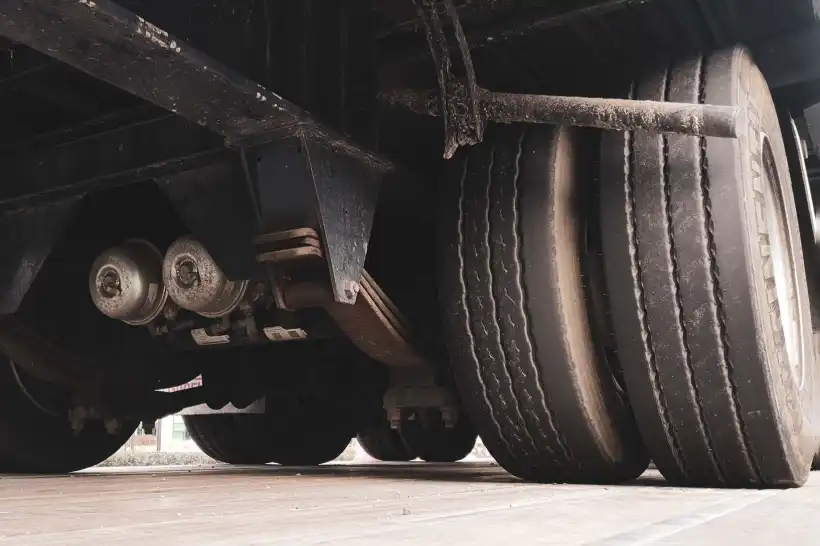
Alignment Mistakes That Shorten Tire Life and Hurt Your Bottom Line
Misalignment is a hidden tire killer. From skipped inspections to rear axle neglect, these costly alignment mistakes slash tire life and drain your budget. Learn how to fix them with routine checks, load-aware adjustments, and smart tracking to protect your fleet.